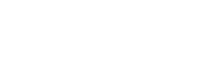
KLEEMAN HELLAS
Development and Investigation of Metal 3D-printed Bioinspired Lattice Elevator Braking Pads for Enhance Dynamic Friction Performance
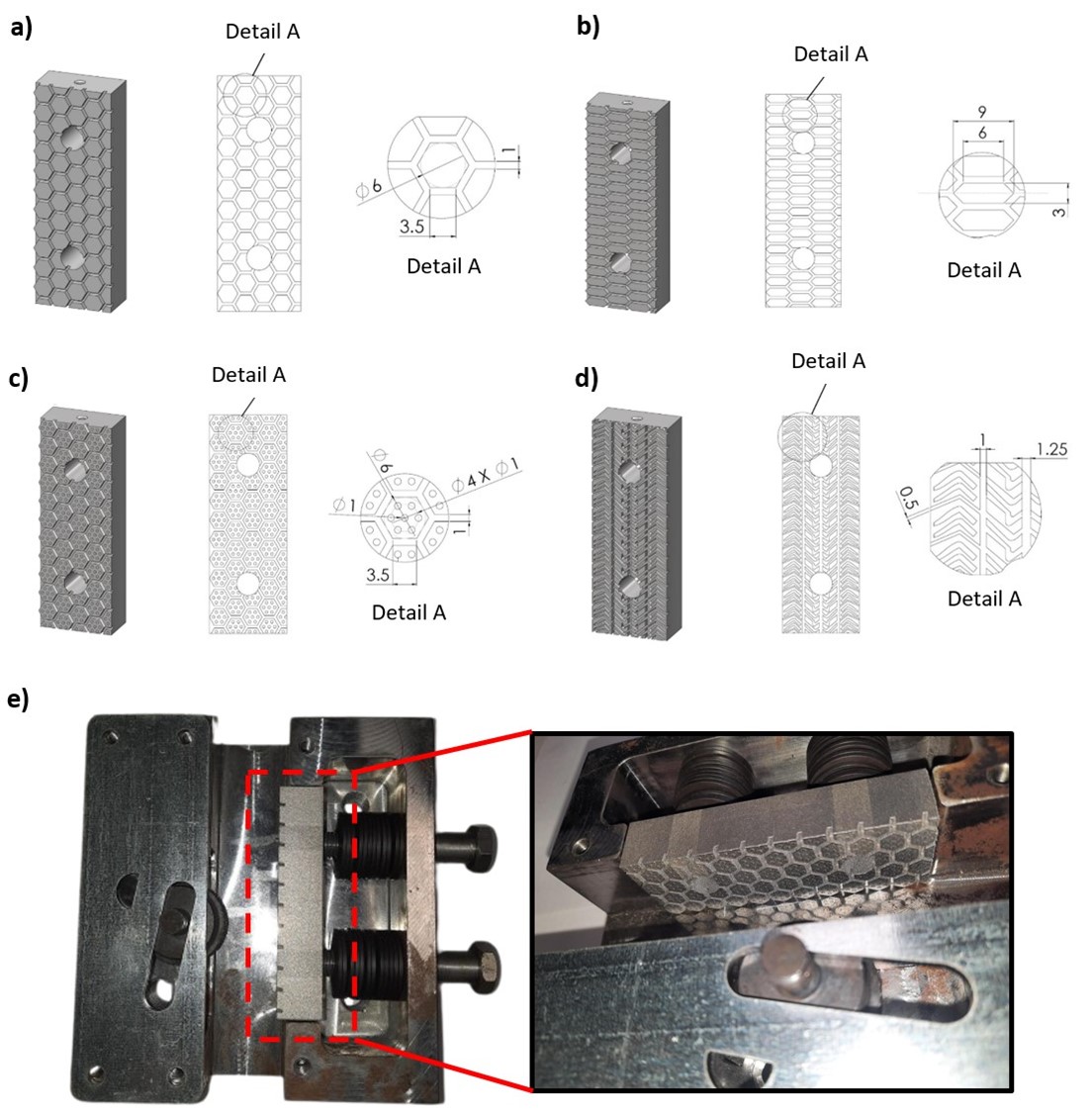
Overview
The project developed four friction pads for an elevator emergency progressive braking system with four different biomimetic hierarchical patterns each on their braking surface. More specifically, the first pattern was the honeycomb structure made up of equilateral hexagons with distinct gaps for the diffusion of foreign bodies (dust, liquids, shavings, etc.) between each hexagon and is shown indicatively in Figure a. The second pattern was the extended honeycomb structure defined as a variant of the biomimetic hierarchical honeycomb structure where the hexagons of the structure have been flattened in one direction in order to increase the available grip/braking area per element and achieve a more compact structure of the elements, is shown indicatively in Figure b. The third pattern was the speckled honeycomb structure which like the simple honeycomb structure is made up of equilateral hexagons with distinct foreign body diffusion channels between each hexagon, with the addition of spots that have been designed in order to create a first zone of light contact with the guide rails leading to smoother deceleration of the chamber of the elevator. Finally, the fourth pattern was a hierarchical pattern which is mainly used in car tires for better grip on the road surface to increase the braking performance, it is clearly shown in Figure d. Then, these patterns were constructed using 3D printing and the Selective Laser Melting (SLM) technique. H13 tool steel was chosen as the construction material so that the produced pieces have enhanced strength and durability. After the 3D printing of the friction pads, a series of tests were carried out to evaluate and certify their functionality and reliability. The first observation was the visual inspection, during which no obvious manufacturing defects and failures were observed. Then, using a high-precision scale, the actual relative density of the produced friction pads was checked against the nominal relative density of the digital models. In this way, the existence and extent of internal porosity in the 3D-printed objects were checked. The measurable relative densities ranged between 99.5%-99.8%, which are within the limits given by the H13 tool steel powder supplier. The range of these values demonstrates the high quality of the 3D metal printing process and the structural integrity of the produced parts as the porosity is less than 0.5%, so potential stress concentration areas are almost negligible. Immediately thereafter, the produced friction pads were tested for fitment/assembly on the existing elevator emergency progressive braking system and for proper operation. As shown in Figure e, the 3D-printed friction pads are perfectly assembled on top of the existing system and allow its smooth operation. Finally, these friction pads were tested in realistic operating conditions by activating the system at speed and progressive immobilization of the elevator car. These tests yielded qualitative results for the 3D-printed friction pads, which demonstrated the correct functionality of the overall integrated system as well as the high braking performance of the friction pads with biomimetic hierarchical patterns on the braking surface.
Services
- Development of friction pads with biomimetic hierarchical patterns for elevator emergency progressive braking systems.
- Construction of friction pads using 3D printing and Selective Laser Melting (SLM) technique.
- Testing and evaluation of friction pads for functionality and reliability, including visual inspection, density checks, fitment/assembly tests, and test in realistic operating condition tests.
- Integration of friction pads into existing elevator emergency progressive braking systems.
Benefits
- Enhanced safety: Biomimetic hierarchical patterns improve braking performance, ensuring quick and efficient emergency stops in elevators.
- Increased durability: Friction pads constructed with H13 tool steel using 3D printing and SLM techniques offer superior strength and durability.
- Reduced maintenance: High-quality construction and proper diffusion channels ensure the proper removal of damaged material and minimize the need for frequent replacements or repairs, saving time and resources.
- Improved reliability: Comprehensive evaluation procedures ensure the functionality and reliability of friction pads, enhancing overall system performance.
Value Proposition
Our solution offers advanced friction pads with biomimetic hierarchical patterns designed to enhance the performance and reliability of elevator emergency progressive braking systems. By leveraging innovative 3D printing and SLM techniques with H13 tool steel construction material, we ensure high-quality, durable friction pads. Our comprehensive testing procedures guarantee functionality and reliability, providing peace of mind for elevator operators and passengers alike. With improved braking performance demonstrated in realistic operating conditions, our solution offers enhanced safety and efficiency for elevator systems.
Find out more
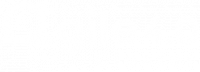
Το έργο Agile4.0-Cluster υλοποιείται στο πλαίσιο της Δράσης ΣΥΝΕΡΓΑΤΙΚΟΙ ΣΧΗΜΑΤΙΣΜΟΙ ΚΑΙΝΟΤΟΜΙΑΣ/ ΣΣΚ και συγχρηματοδοτείται από την Ευρωπαϊκή Ένωση και εθνικούς πόρους μέσω του Ε.Π. Ανταγωνιστικότητα, Επιχειρηματικότητα & Καινοτομία (ΕΠΑνΕΚ).
Το έργο ξεκίνησε τον Αύγουστο του 2020 και αναμένεται να ολοκληρωθεί τον Αύγουστο του 2022.
Επιστημονικός υπεύθυνος είναι ο Δρ. Δημήτριος Τζοβάρας από το EKETA / ΙΠΤΗΛ.
Επικοινωνία
-
Ινστιτούτο Τεχνολογιών Πληροφορικής και επικοινωνιών
Εθνικό Κέντρο Έρευνας & Τεχνολογικής Ανάπτυξης,
6o χλμ Χαριλάου - Θέρμης, 57001, Θεσσαλονίκη - Dimitrios.Tzovaras@iti.gr
- +30 2311 257 701-3